Magneto inductive equipment is made for inspecting the inner and the outer part of ferro-magnetic ropes. The MRT equipement is mainly composed by two elements:
- the measuring head
- the acquisition system.
In this article, you will learn the basic structure of this inspecting tool
1. Measuring head
The measuring head or detector is the part of the equipment that is mounted on the rope to test. Measuring head entails magnetic circuit and sensors. Magnets induce a magnetic flux inside the rope to fully saturate it. Neodymium-Iron-Boron (NdFeB) magnets ensure high performances in terms of magnetization, this characteristic allows to minimize measuring head dimensions and weight.
The magnetizer induce a strong magnetic inside the rope, if there are no defects, the magnetic flux flows without interruption.
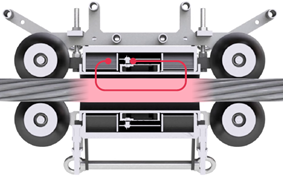
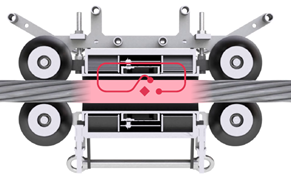
When broken wires or defects occur, a modification of the magnetic flux lines appears and leakage flux born. This magnetic field change, in value and direction, is detected by sensors placed around the rope that translate the physical phenomena in a readable signal. The closer the sensors are to the rope the better is the result in term of sensitivity.
Usually the measuring head is designed for a certain rope diameter range. Weight and dimensions are strictly linked to the size. Depending on the inspection environment the shape of the device varies. The standard configuration for mobile application is a close architecture in wich both magnetizer and sensors enclose the rope, whilst in the cableway sector for hauling ropes an open architecture is preferred because the device must pass on cableway clamps.
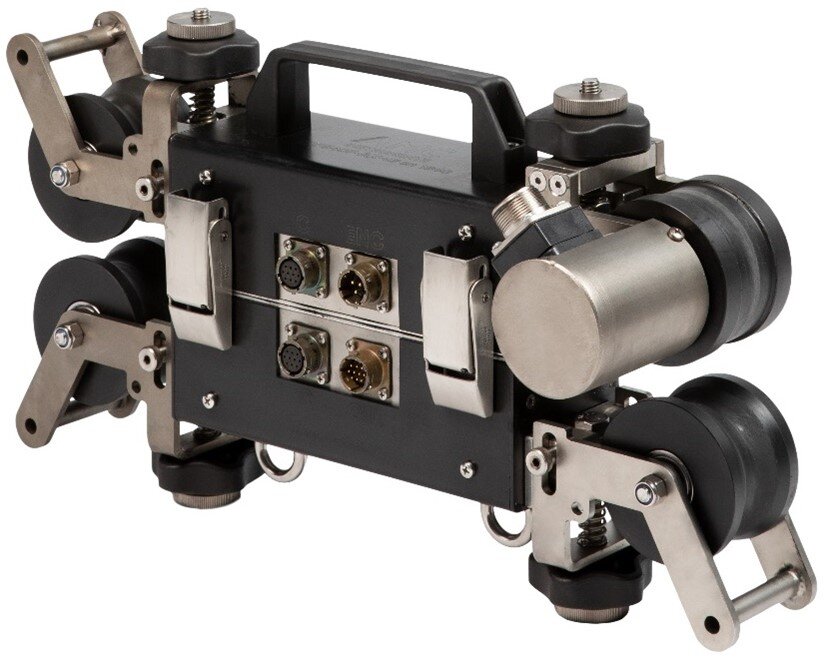
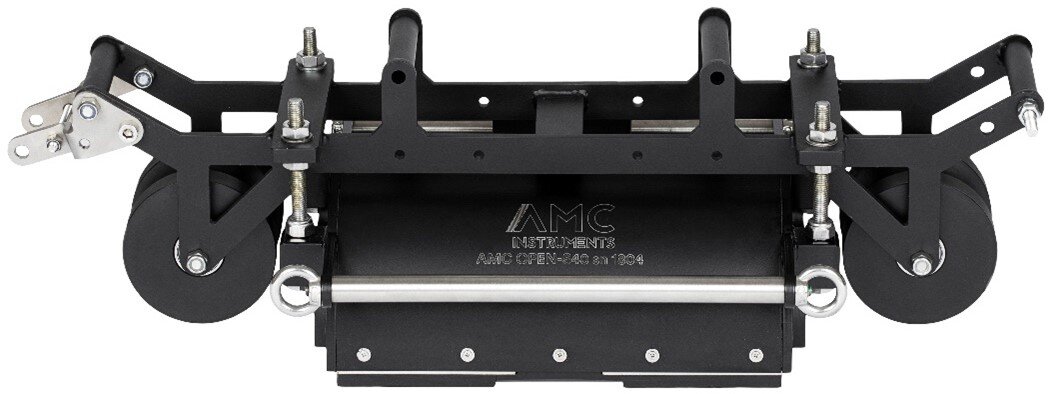
Both configurations allow the technician to inspect specific diameter range. To detect lower diameter range is is suggested the use of a reduction bushing kit.
2. The acquisition system
This part of the equipment is made of a data processor and a software for the interpretation. The acquisition system transforms the sensor’s inputs in a signal on a graph allowing the user to acquire, save and perform interpretation. Sampling rate per channel and resolution bit are key characteristics for designing the data processor, the higher is the sampling rate per channel the better will be the digital signal construction. The software is the human interface of the system and it must be provided with a deep training in order to avoid misinterpretation and wrong filtering. Real time acquisition is a mandatory feature to perfectly follow the ISO4309 during the inspection.
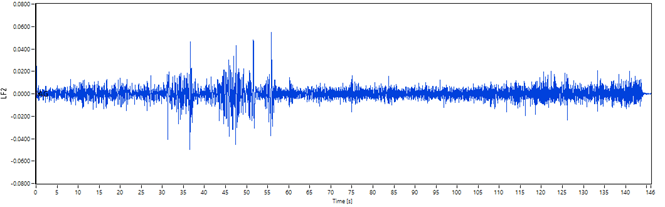
The acquisition system is usually made of a data processor and portable computer, where the software is installed. Depending on the inspection environment we suggest two different configurations:
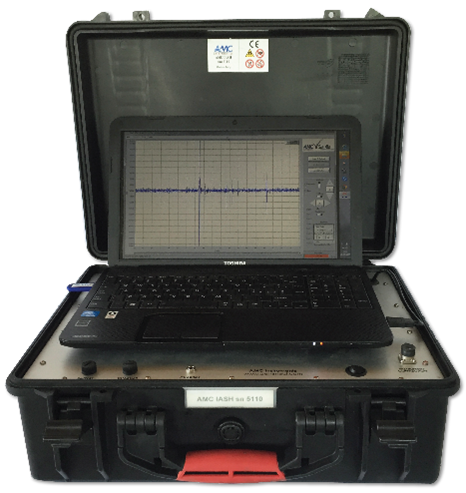
IAS-H
A rugged case with a pc highly suggested for complex inspection environment such as Offshore, Harbour, construction sites.
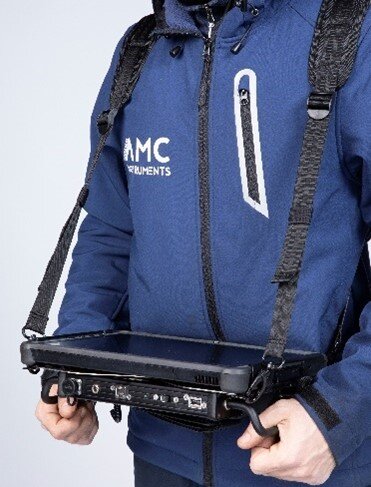
IAS-T
A rugged tablet integrated with a data processor, highly suggested for inspection with almost no room for movement such as crane basket.
More about Magnetic Rope Testing?
Discover our articles about this unique steel wire rope inspection methode:
- Visual inspection VS MRT inspection
- Rope inspection, safety and the ISO4309 regulation
- To LF or to LMA? That is the question!
- The importance of interpretation
- IOT and wire ropes
- High magnetization VS low magnetization
- The EN12927, is your MRT device in compliance with the standard?
- 8 Fundamental points to correctly choose an MRT device
- 3 Steps to develop customized magneto-inductive equipment