A design customization is a more and more frequent necessity to avoid standards and interface complexity.
The technical maturity of the magneto-inductive methodology (60 years) and its inspection adaptability to any ferromagnetic materials create the best conditions for customization. The magneto-inductive method has been used in different sectors and applications, cableways, cranes, belt conveyors, elevators and pipes, helping the maintainers to have a complete picture of the inspected object. The magneto-inductive method, thanks to its accuracy and reliability, it is claimed by : EN12927 (Cableway); ISO4309 (Heavy Lifting); UNI 1607593 (Elevator Technical Project).
In this article the reader will know which the main steps are to realize a customized product.
1. Feasability study
The customer and the designer must create a working path to achieve the desired goal. Getting off on the right foot requires cooperation and a clear communication. The customer should describe the whole working environment, highlighting the needs for developing a customized product. The Mining, The Offshore and the Elevator Sector are perfect example of complex environment characterized by not ordinary inspection conditions.
It is fundamental to define with the customer a set functions that the tool must perform and an acceptable range of price. Once all this information has been collected, the technical and the commercial team will prepare a quotation and the relative technical projects. These two documents are interdependent, constituting the customization project. If the project is accepted a time-plan will be released.
2. Designing and producing the customization
In this phase information flows fast. The technical team, when it is possible, will perform a site-inspection to collect all the required data. A 3D model will be elaborated to show the customer the work done and to be completely sure that everything will be made according to the specifications.
This model will be the base for the equipment production. The customization can entail both the hardware (measuring head, acquisition system) and the software or just one of them.
3. Installation, calibration and training
The product will be delivered with the relative instruction manual. Specially when we are talking about permanent installation, Calibration and Installation are the most delicate phases. They represent the final validation process for the whole equipment and its connections: Measuring Head – Acquisition System – Software.
You will know see an example of the development of a permanent installation device to inspect continuously from 1 to 8 elevators of 6 ropes each.
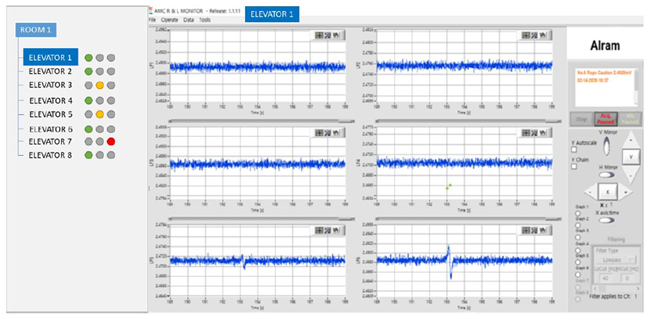
Customized Software
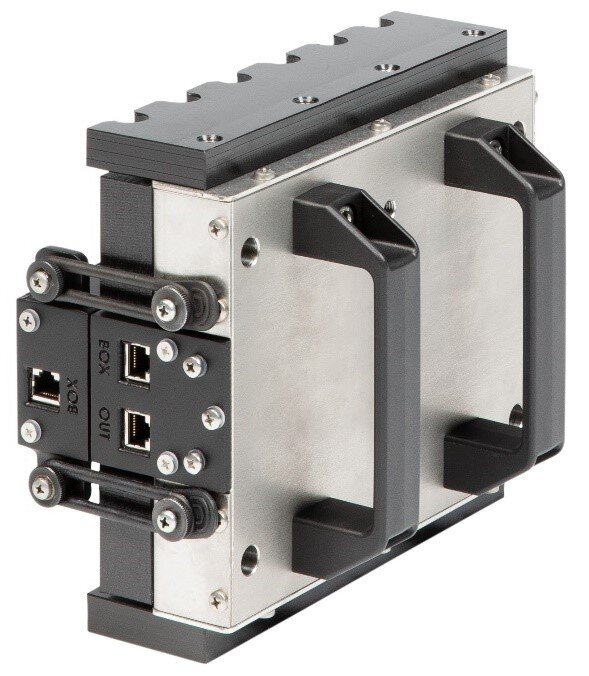
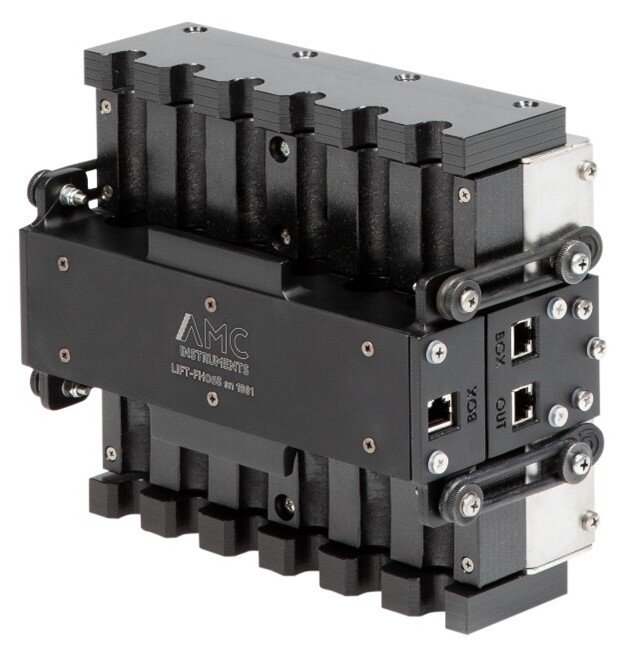
Permanent Measuring Head for a specific Elevator
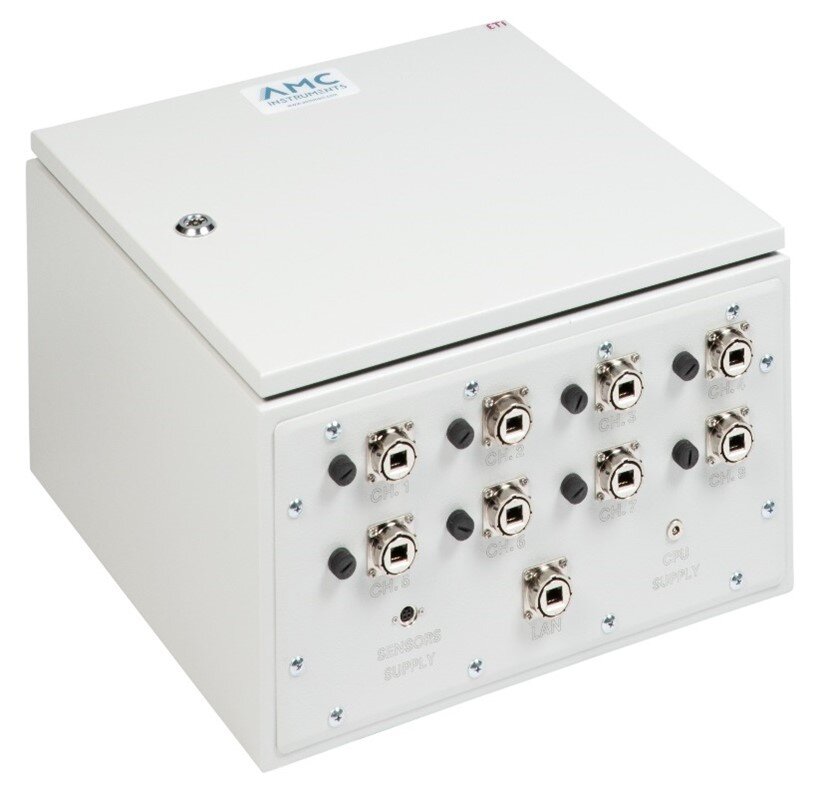
Acquisition System able to acquire 8 different measuring heads