How can a competent person decide which is the best assessment method for each defect?
The visual inspection can be defined as the first assessment method for a correct metallic wire rope evaluation. The method consists of deeply looking at the rope, searching for deterioration modes and reporting the results on a document.In all the updated versions of the ISO4309, the visual inspection has always been considered the principal or the only inspection tool, even if in the last releases the MRT is included.
It must not be confused with a simple search for macro-defects, it is a very delicate operation and it should be performed by a competent person. A good technician must recognise different defects typologies such as broken wires, valley breaks, waviness etc. This kind of inspection can require hours, depending on the rope and inspection conditions.
How can a competent person find the defects on the rope?
Some defects are usually visible and easily recognisable with a visual inspection, for the most hidden ones a MRT should be necessary.
1. Protrusion
The picture below shows a Core protrusion, it can be caused by shock loading as well as improper installation. Rotation-Resistant wire ropes on hoists must be installed with extra care and proper handling to prevent rope damage during installation.
By introducing twist or torque into the rope, core slippage may occur and it might protrude from the rope. This protrusion is an example of macro defect and it is enough to discard the rope.
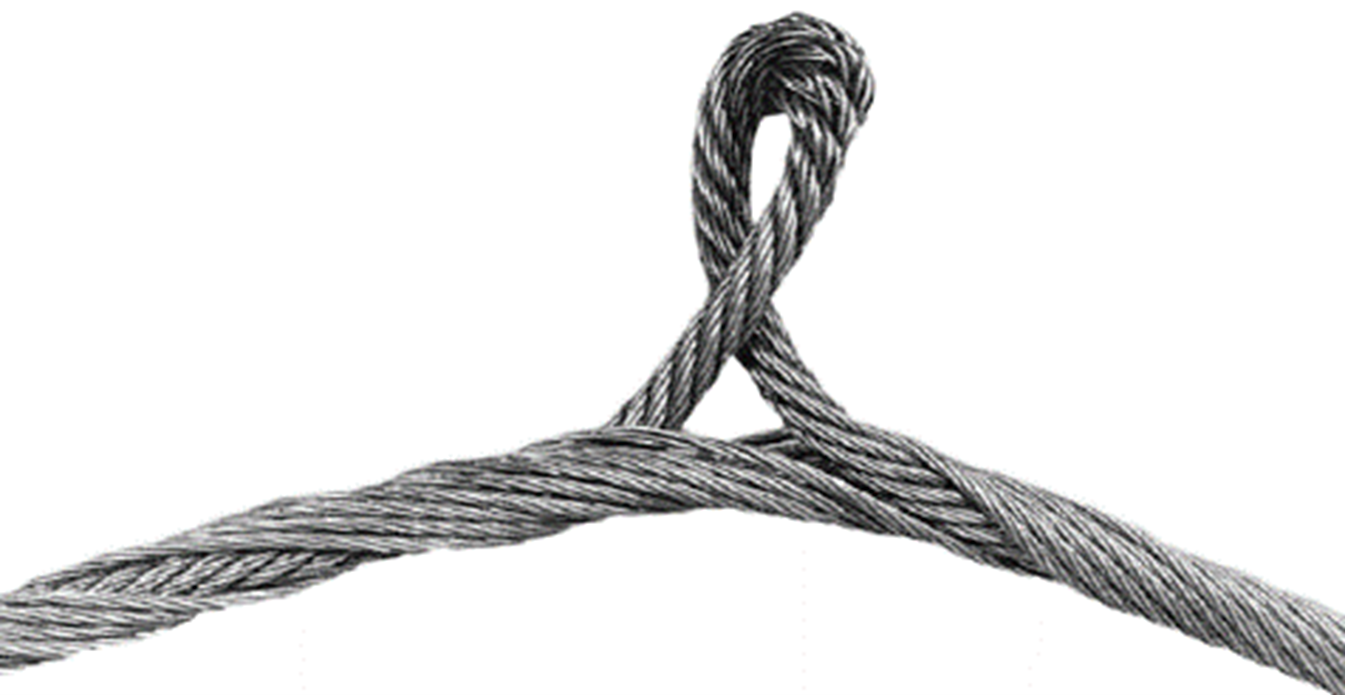
2. External fatigue broken wires
In the picture below we can see a group of external broken wires, the square ends of wires suggest they’re fatigue breaks.
Hoists wire ropes are subject to a lot of repetitive bending over sheaves, which causes the rope to develop cracks in its outer wires. The smaller the sheave is in relationship to the diameter of the wire rope, the higher the bending fatigue. Once broken wires start to appear, they create a domino effect and much more will appear shortly.
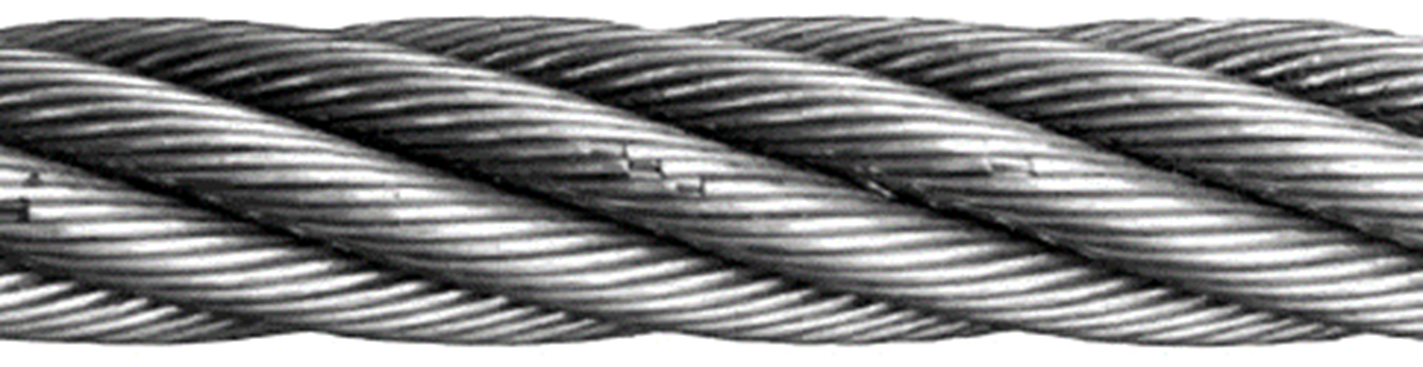
This kind of defect can be identified through a deep visual analysis but grease, lack of light and inaccessibility can prevent the detection, in these cases they can be more easily remarked by a MRT. In fact, although defects could be clearly visible in some situations and almost invisible in others, they still remain.
3. Valley Breaks
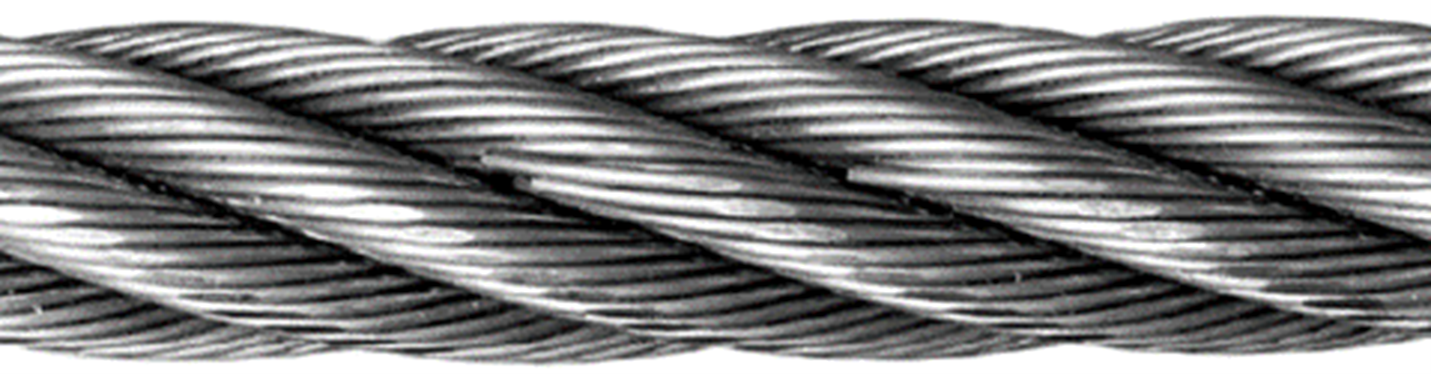
A valley break is a special defect and it is quite difficult to identify, because the breakpoint is usually located in the valley region between the strands. Valley wire breaks typically occur due to inter-strand nicking deriving from the forces between strands while the rope is under bending load, during spooling and when running over sheaves.
This phenomenon is usually very dangerous because the presence of valley wire breaks is a strong indication of internal deterioration in a wire rope.
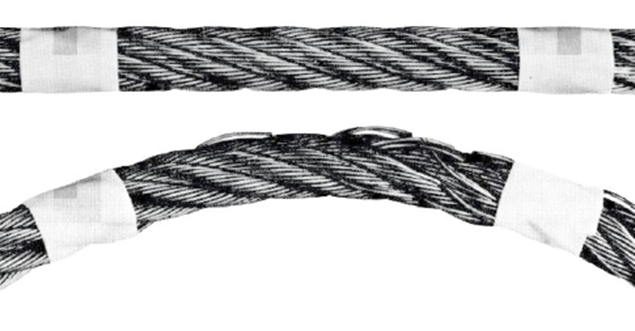
Flexing the rope exposes hidden broken wires and while doing that, you may hear cracking sound from inside the wire rope. Of course bending the rope is not always possible, in this case a Magnetic Rope Test might be very useful to detect them.
4. Internal defects
In some types of wire ropes most of the defects are internal. In low-rotational ropes this happens very often and the standard ISO4309 as well describes this phenomenon.
The picture shows a low-rotating wire rope before and after the external layer of strands has been removed.
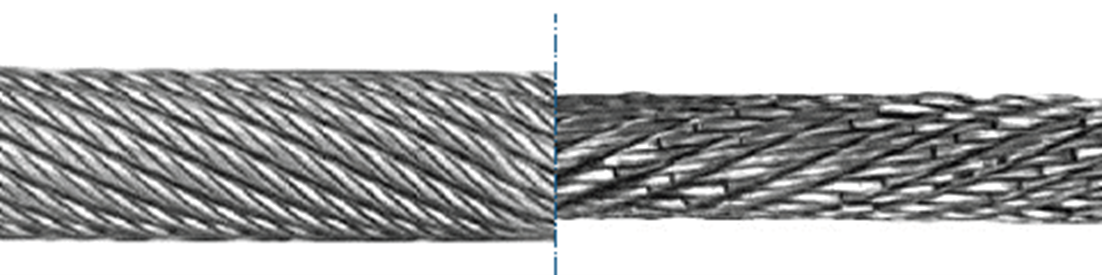
On the left side, the external layer has no defects, whilst on the right side the internal layer is full of broken wires. In this case visual inspection is not the correct method to evaluate the rope condition, a MRT is needed.
5. Internal corrosion
Internal corrosion is not so easy to find, it can be visually detected when a red powder is coming from the inter-strand zones of the rope. Unfortunately, this is not enough to evaluate the rope conditions because rust can also come from other parts of the plants, like sheaves and drums.
Watch out! This kind of defect can be critical in real applications, when suspecting internal corrosion is better to perform a MRT.
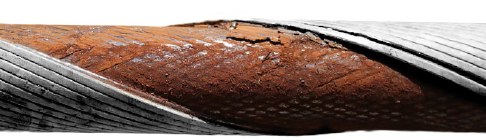
When is a MRT suggested?
The Magnetic Rope Test is suggested every time the Visual Inspection is not enough for a correct wire rope evaluation.
This picture shows a diagram corresponding to a magnetic rope test in a marine environment. The whole rope was covered with lubricant and was very difficult to perform an in-depth visual inspection.
The visual inspector did not find any problem and the rope has been declared in good conditions but, when a MRT has been performed, it highlighted a different condition.
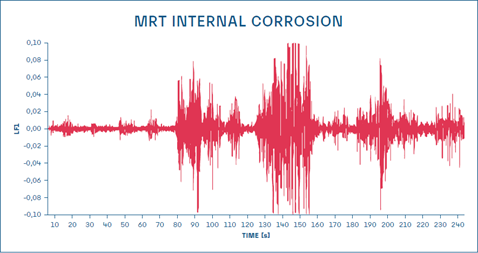
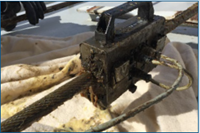
The diagram reveals a very dangerous situation, there are some zones with a high peak concentration and this means that the rope is deeply corroded.
The rope has been immediately removed and a breaking test has been performed. The result shows that the residual load capacity was less than 1/3 of the nominal one (125kN vs. 400kN).
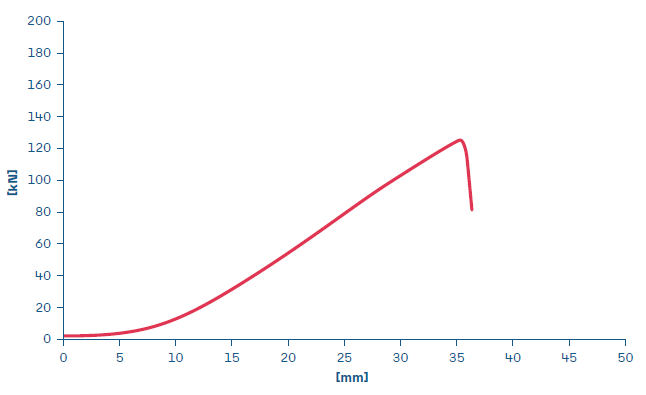
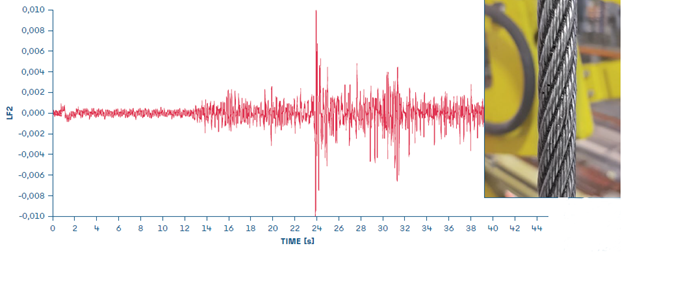
In this other picture the MRT diagram of a crane rope is shown. This plant is working 24/7 and the rope get damaged very quickly; for this reason the device is always mounted on it to ensure a continuous monitoring.
In this case it’s easy to find broken wires on the rope surface but it requires long plant stops. The MRT is useful to detect every defect on the rope, to monitor the situation and to schedule the plant stop and the rope replacement.
Conclusions
It is important to focus on the meaning of “visible”, which strongly depends on the inspection conditions, grease, speed, operator’s attention.
For external defect an MRT is not mandatory, but it is the only tool that can provide a quick and accurate assessment of whole rope conditions.
For internal defects, the situation changes. MRT is the only method claimed by regulations (EN12927, ISO4309).
When it is not possible to perform a Magnetic Rope Test, the inspector must evaluate the rope conditions just basing his assessment on the visual inspection and his own experience.
To have a clear vision of all the different modes of deterioration and the relative assessment methods we suggest you check on the ISO4309.

More about Magnetic Rope Testing?
Discover our articles about this unique steel wire rope inspection methode:
- Rope inspection, safety and the ISO4309 regulation
- To LF or to LMA? That is the question!
- The importance of interpretation
- IOT and wire ropes
- How is MRT-equipment made?
- High magnetization VS low magnetization
- The EN12927, is your MRT device in compliance with the standard?
- 8 Fundamental points to correctly choose an MRT device
- 3 Steps to develop customized magneto-inductive equipment
Q&A Webinar: discard, Inspection and MRT
ISO4309 is only for steel wire rope running on steel sheaves. There are no regulations so far for plastic sheaves. In many casses the sheaves are changed together with the ropes and this avoids a lot of discussions. We never had an answer from plastic sheave manufactors on this matter. A lot of inspectors use the standard norm since there are no other norms on this. But they are buiding up experiences which could be useful to make a separate norm.
Yes, you need to discard if you find 2 valley breaks on 6xd (= 1 lay lenght)
In most cases too narrow grooves in sheaves or drums can cause valley breaks. New rope with standard tollerances of +3,5% in worn out grooves from the old rope, new rope will be pushed in to narrow groove and the rope will make a new groove, but will be destroyed inside. Outer strands are squashed on the steel core. Indentations underneath the outer strand will lead to valley breaks between and under the strands.
In the Netherlans the EN3233 was used for years by experienced people – and still today used as a guidance next to the ISO4309. The figures in the tables will differ a bit but in the end the discard will be almost the same. Problem was that the discard criterium about wear was not always clear and could lead to discussions.
Yes if there is 1 valley break in 1 laylength, discard or further inspections are needed. Discard if 2 valley breaks like noted in the standard ISO4309.
One broken wire has 2 broken ends, but is counted as only one broken wire. See also foot notes in the norm ISO4309.
No this is for running ropes over sheaves.
Everything in nuclear working environment is special. Please inform yourself in the country of application. We would advise also MRT to be 200% sure.
Yes. The MRT can detect both internal and external defects.
The combination between MRT and Visual Inspection is the most accurate technique to find defects. MRT is very accurate to find broken wires, corrosion, distortion. Also visual Inspection is accurate (only for external defects) if it is performed in the correct way. Often, this is the point. If visual inspection is not performed in the correct way, MRT is certainly more accurate.
It is not right to say that ISO4309 only reccomends MRT. ISO4309 indicates MRT as one of the assessment methods to be used for some kinds of modes of deterioration. The regulation says that if you want to perform an internal inspection, you can use clamps only if you can not use MRT. The regulation says that you have to evaluate internal corrosion and if you do it without MRT, this will be qualitative. The regulation says that in non rotational ropes, the most part of the defects can appear internally. The regulation gives you the ‘instruments’ that you can use to perform your inspection. Then, it is up to you.
No. Stainless steel is not magnetic.
Yes. Here the device will move along the rope.